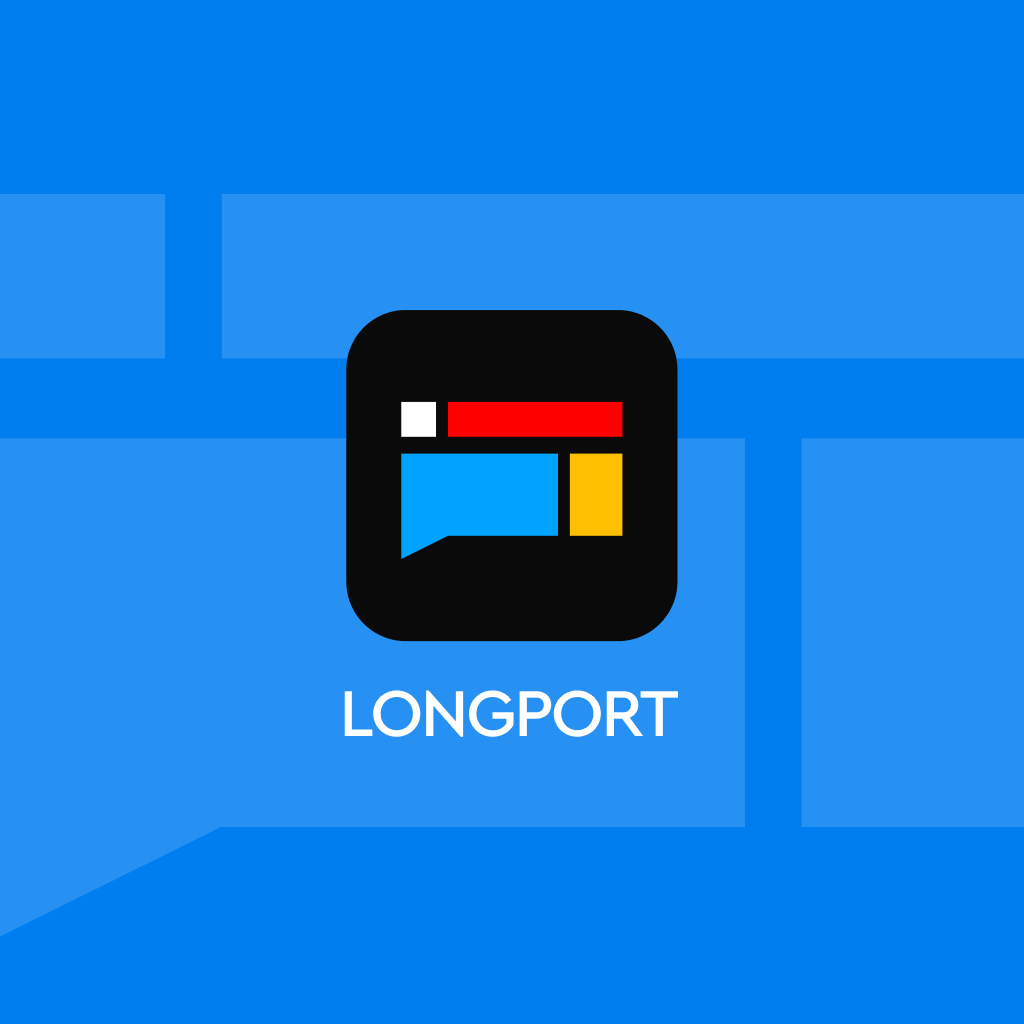
Apple's black technology in Vision Pro, China is about to occupy the technological high ground!
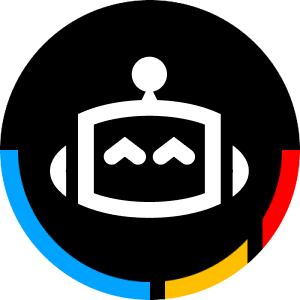
BOE, Samsung Electronics, and LG are all seen as potential suppliers for the next generation of Vision Pro micro displays, breaking Sony's monopoly.
Apple launches Vision Pro to bet on MR, injecting a shot in the arm into the leaderless mixed reality industry.
The two Micro OLED displays exclusively supplied by Sony are like a shot of adrenaline, pointing to a clear but short-lived direction for the fiercely competitive micro-display market.
In the fierce battle between Fast LCD and Micro LED, Micro OLED has won a breathing space.
Fast LCD is much cheaper than Micro OLED, but its technical specifications are not as good as the latter.
Micro LED has comparative advantages in technical specifications, but full-colorization and mass production are difficult problems.
Micro OLED has been steadily developing for more than 20 years, with mature technology and stable yield. Although there are many Micro OLED suppliers around the world, Sony's technology and production capacity are relatively high, making it the exclusive supplier of Apple's Vision Pro.
micro LED
Before 2019, Sony had already established mass production technology for Micro OLED. Head-mounted displays were not their main customers, but Sony's own mirrorless cameras were their biggest customers. At that time, mirrorless cameras were rapidly eating into the SLR market. In addition to their small size and portability, the use of Micro OLED electronic viewfinder components allowed cameras to achieve the same effect as optical viewfinders even without a reflex mirror.
In 2019, Sony further introduced micro-lens array technology (Micro Lens Array, yes, the same technology used by LG G3 this year), which increased the brightness from the previous 1800nits to 3000nits, and even reached 5000nits (the same level as Apple's Vision Pro) in 2021.
High precision, high brightness, stable production capacity are some of the reasons why Sony is favored by Apple.
However, Micro OLED is not Apple's ideal choice. Cook's preference is Micro LED.
In 2014, Zhang Shichang, Apple's director of display technology research and development, took a team of 50 elite researchers from AU Optronics (hereinafter referred to as "AUO") to fully develop the next-generation display technology, Micro LED. Regarding this, the Chairman of Longbridge Dolphin, Peng Shuanglang, casually stated that he was not quite sure. Apple has a supply chain all over the world, so there is nothing strange about poaching talent from Taiwan.
Longbridge Dolphin is not the only supply chain manufacturer that has been poached. Zhang Shichang's list also includes companies such as Innolux, Chunghwa Picture Tubes, and even doctoral graduates from the Organic Optoelectronics Laboratory at National Taiwan University. All personnel are stationed in the Taoyuan Longtan Science Park, 27 kilometers away from Taipei, and are protected by former FBI personnel from the United States. Their security measures are as strict as a piece of land belonging to Apple in Taiwan, China. Why Taiwan, China? Let's start with a small American company called LuxVue. Founded in 2009, this small company is dedicated to miniaturizing LEDs and mass-producing display devices with this technology. This idea seemed unattainable at the time, but it attracted the attention of many Taiwanese manufacturers who were lagging behind Korean companies in competition and urgently needed new technology to gain an edge.
Longbridge Dolphin, MediaTek, Chilisin, and Crystalwise, other leading Taiwanese manufacturers, successively invested in LuxVue, which also set up its supply chain in Taiwan, China, to help cultivate new technology talents in Taiwan, China. This is a story of mutual benefit.
It can be said that Taiwan, China is where the Micro LED dream began.
In the Taoyuan Longtan Science Park, there is TSMC's most advanced packaging plant and Longbridge Dolphin's panel plant, which can provide testing and assistance to Apple's R&D team at any time. Coupled with the LuxVue technology that Apple acquired at four times the price of its competitors in the same year, Micro LED was all the rage, and it was rumored that it would soon appear on Apple's product list.
But as the saying goes, the greater the expectation, the greater the disappointment.
In the past decade, Longtan's secret special forces have been shuttling back and forth between Taiwan, China and Silicon Valley, but they have not yet produced what Cook wants.
There are two bottlenecks for Micro LED. The first is full-colorization. Most of the Micro LEDs currently in mass production are presented in single green, such as Xiaomi's smart glasses. The problem of the efficiency of red light LEDs still exists. In addition, the current design of the driving circuit presents significant challenges for driving RGB three-color Micro LEDs with different currents.
However, the more difficult challenge is mass transfer, which requires a high yield rate for each Micro LED chip.
The process of making Micro LED is achieved by using photolithography technology on a gallium arsenide (GaAs) substrate, and it must be further processed by physical or chemical methods to transfer it from the GaAs substrate to the silicon substrate. This process involves the transfer of millions of Micro LED chips, hence the name "mass transfer".
Currently, the yield rate of Micro LED chips can reach 99.9%, which means that only 1 out of 1000 chips is defective.
Sounds great, right?
A 2K resolution Micro LED display requires 6 million chips, which means that, according to a yield rate of 99.9%, there will be 6000 defective chips!
As the saying goes, "a miss is as good as a mile". Our Chinese ancestors from thousands of years ago already saw through the production difficulties of Micro LED. It's really impressive!
In short, in order to achieve mass production of a Micro LED display, the yield rate before mass transfer must exceed 99.9999%, which means that there can be at most 1 defective chip out of 1 million chips, not to mention the success rate of mass transfer.
The world is so cruel. Problems that can be solved with money are not problems. As for those that cannot be solved with money, they become historical problems.
In the face of the production difficulties of Micro LED, Apple's financial power has also failed.
Therefore, Apple turned to Sony and purchased the latter's Micro OLED panels. According to a VisionPro teardown report widely circulated in the industry, the cost of this screen is estimated to be as high as $300, accounting for nearly 20% of the total cost.
Sony's technology is not the most powerful. Its Micro OLED structure is in the form of white light + filter, which has two disadvantages:
First, the blue light OLED material required for white light OLED has low luminous efficiency and short lifespan.
Second, at least 2/3 of the original brightness will be absorbed by the filter, resulting in low efficiency of the entire optical system and seriously affecting the brightness performance.
Brightness is crucial for MR and AR devices. This is because AR requires the introduction of ambient light, which involves the performance of ACR (Ambient Contract Ration), while VR devices do not have this requirement.
eMagin's dPd technology (Direct Patterned Display) is highly anticipated. It uses true RGB three-color OLED luminescent materials, without the need for filters, completely freeing the brightness seal. In terms of technology, the dPd technology does not use fine metal masks, but directly deposits RGB luminescent materials on CMOS silicon, which eliminates the refinement that has been delayed due to the metal mask process.
Currently, eMagin has developed the brightest full-color Micro OLED display to date, with a brightness of up to 15,000 nits.
eMagin's weakness is production capacity. Its factory in Dutchess County, New York, has an annual production capacity of only 50,000 to 60,000 pieces, which is far from meeting Apple's demand.
How big is Apple's appetite?
900,000 pieces a year!
This is the maximum number given by Sony, and Apple's demand is much greater than that, but Sony is not willing to expand production capacity, even for Cook's sake. The specific reason is unknown.
In fact, Sony's Micro OLED annual production capacity was originally expected to be less than 800,000 pieces. The MicroOLED display screen of Vision Pro is 1.42 inches, with a resolution of 3600×3200 and 3400 ppi. However, there is no corresponding specification in Sony's product list. There is reason to believe that this display screen was specially customized by Apple.
Customization + maximum production capacity, Sony has given enough face, after all, it is an order worth up to 270 million US dollars, equivalent to 37.6 billion yen. In comparison, Sony's net profit for the whole year of 2022 is only 937.1 billion yen.
With more than 200 billion US dollars in cash, can Apple not explode the production capacity of Micro OLED if it can't explode Micro LED?
Sony's competitors are also watching closely.
Chinese manufacturers are also experienced in the field of Micro OLED, and their technical level is not weaker than that of foreign leading companies.
Visionox has a product with a 1.3-inch, 3.5K resolution, and 4000 nits brightness, and has mastered the RGB Micro OLED process technology. Its 12-inch (wafer cutting size, not product size, the same below) production line has reached 72,000 pieces/year (referring to wafer capacity, can produce 20 million display screens according to official data, the same below), and is in a leading position in China.
BOE has a product with a 1.3-inch, 4031ppi, and 5000 nits brightness, and has 8 and 12-inch Micro OLED production lines, with a combined capacity of up to 30,000 pieces/year.
Lakeside Optoelectronics, which collaborates with Kopin and Panasonic, Huaxing Optoelectronics under TCL, and Kunshan Dream Show under Visionox, are all striving to increase production capacity.
Leading Korean companies in this field have been slow to respond, with Samsung and LG having trial products but no production lines. The former is expected to enter Apple's supply chain by acquiring eMagin and is expected to do so by 2024. The latter is partnering with Meta and SK Hynix to obtain funding and wafer production lines.
BOE, Samsung, and LG are all potential suppliers of the next-generation Vision Pro micro display, breaking Sony's monopoly.
Apple never puts all its eggs in one basket, unless it has no choice.
Don't forget, Apple also has Micro LED as the ultimate option, with brightness, power consumption, and lifespan all superior to existing MicroOLED technology.
Traditional home appliance giants Sony, Samsung, and LG have all laid out their plans, while internet giants Apple, Meta, and Google have each acquired relevant technologies through acquisitions.
Foxconn is also very interested in this and has joined forces with Sharp, Innolux, and Radiant Opto-Electronics to invest in the US Micro LED company eLux. This decision is closely related to Sharp's breakthrough in this field.
Sharp developed a full-color Micro LED display in 2019, with a size of 0.38 inches, 1053ppi, and 1000nits. This product uses blue Micro LED, which is converted into red and green light through quantum dots, and then purified through a filter, and is expected to be mass-produced in 2023 or 2024.
In addition, eLux has a close relationship with Sharp, with its CEO and CTO both coming from Sharp's US laboratory. With this relationship, Foxconn may also want to use Micro LED technology to win another Apple order.
Fast LCD has an unshakable position in the VR field, with a market share of up to 98%, used by Oculus Quest 2 and ByteDance Pico 4.
In the AR field, Micro OLED has the advantage, with a market share of 64%, followed closely by LCD with only 9%.
Micro OLED is in an awkward position, with almost no presence in the VR field, and although it is currently dominant in the AR field, it also faces the threat of Micro LED catching up.
Apple's personal involvement in Micro LED shows that this is the best solution for Cook.
For Micro OLED to survive, it is not only a race against time, but also a race against Apple.